- Mainpage
- Directory
- Non-ferrous metals
Duralumin
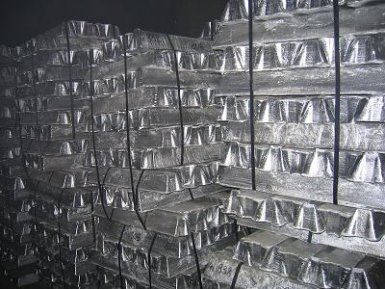
General characteristics
Duralumin (or equivalently, made of anodized aluminum) — wrought aluminium alloy with added magnesium and copper. Buy it today is not difficult. The price depends on the percentage of components and additional conditions of delivery.
The main alloying elements are Mn, Cu and Mg. Copper usually contains a 4.4%, manganese — 0.5%, magnesium 1.5 per cent. Magnesium and copper is used to give the alloy strength. Manganese, due to its properties, refines the structure, thereby increasing corrosion resistance and strength. In addition to these elements, the composition used and even silicon and iron. Fe is considered a harmful impurity, reduces the strength and ductility. Si helps to reduce the harmful effects of iron, to a certain extent, tying it. The melting point of the alloy is 650 degrees.
The percentage composition of the alloy D 16
Fe | Al | Cr | Mn | Cu | Zn | Mg | Si | Ti+Zr | Impurities |
---|---|---|---|---|---|---|---|---|---|
≤0,5 | 91−94,7 | ≤0,1 | 0,3−0,9 | 3,8−4,9 | ≤0,25 | 1,2−1,8 | ≤0,5 | ≤0,2 | 0,15 |
Dignity
1. The ease of machining distinguish duralumin alloy from the others.
2. Structural strength is also one of the benefits. To achieve it use heat treatment.
3. It is very light alloy. Its density per cubic meter — 2500−2800 kg.
Disadvantages
First, the high sensitivity to sharp notches. Second, a significant decrease of the strength characteristics at higher temperature above 140 °C. third, In comparison with aluminum, duralumin has a lower degree of resistance to corrosion. Sensitivity to corrosion is especially pronounced under stress., This shortcoming has learned to eliminate plating. Pure aluminum is applied to the surface of the alloy with a thin layer of hot method. Cladding method allows to obtain a corrosion-resistant durable material.
Assortment
Duralumin today are widely used for industry, construction, mechanical engineering. Conventionally, it is divided into four groups, depending on the saturation components, which affects the final price.
1. Classic grade D1. The percentage has not changed since 1908, from the moment of the first heats.
2. High-strength grade D16. Strength gives high magnesium content.
3. High heat resistance, brand ВД17 and D19. Have a high content of copper and manganese.
4. Increased elasticity brand D18. Plasticity is achieved due to the increased proportion of magnesium and copper.
The percentage composition of the alloy D 1
Fe | Al | Cr | Mn | Cu | Zn | Mg | Si | Ti | Impurities |
---|---|---|---|---|---|---|---|---|---|
≤0,7 | 92−95,5 | ≤0,1 | 0,4−1 | 3,5−4,5 | ≤0,25 | 0,4−0,8 | 0,2−0,8 | ≤0,15 | 0,15 |
The percentage composition of the alloy D 18
Fe | Al | Cr | Mn | Cu | Zn | Mg | Si | Ti | Impurities |
---|---|---|---|---|---|---|---|---|---|
≤0,5 | 94,35−97,6 | ≤0,1 | ≤0,2 | 2,2−3 | ≤0,1 | 0,2−0,5 | ≤0,5 | --- | 0,15 |
Heat treatment
Annealing. The alloy is heated to t° to 500 °C, with cooling it becomes flexible, similar to pure aluminum. After the aging process of the leading features of dural be the hardness and stiffness. To perform the natural aging requires about a day and a working temperature of 20 degrees Celsius. For artificial aging need a higher temperature, but the time is much less. At the end of the dural technology becomes sufficiently strong and reliable metal that you can use the highest loads. After annealing achieved great plasticity, and after aging a significant samopoznanie.
The ability to samopoznanie at dural was opened by accident and is now often used in the processing material for use in modern industry. Semi-finished products dependent on the technology of production supplied in the artificially aged, hardened and annealed types. The heat treatment in this case is very different — it depends on the structure and thickness of the alloy. After hardening alloys are hardened, but at the same time maintain a high plasticity, which allows them to be subjected to any deformation. Therefore, a drift, punching can be produced at one time. It should be noted that natural aging after deformation reduces the tensile strength of 2 kg/mm2 compared with the strength of those parts where aging has occurred after the required deformation. It turns out that the technology requires deformation of the alloy D1 only in the fresh state hardened, and in the first two hours after quenching. And alloys D16 and D6 require treatment during the period 30 minutes after quenching.
Application
Mechanical engineering, aircraft building, production of high-speed trains, construction of residential or industrial premises. A preferred use of this alloy is due to its larger compared to the aluminum hardness. The most widely used are uterine D16 and D1. They were literally indispensable to aviation. Alloy D1 is considered to be one of the major in the manufacture of pipes, profiles, sheets, wire, forgings, stampings. The same semifinished products made of D16 alloy (except stampings and forgings). D18 (high plasticity) is used in the aircraft industry for the manufacture of rivets. D19 and ВД17 used for the production of deformed semi-finished products. which operate at elevated temperatures. V95 is indispensable in the form of extruded sections, bars and forgings.
Our company «AVEK global» you can order any products and to answer any question regarding the implementation of metal.
Buy at best price
LLC «AVEK global» sells metal on the most favorable terms. In stock provided a range of semi-finished products made of aluminum. From order volume and additional conditions of supply depends on the price. When wholesale purchases enjoy significant discounts. Our managers are always ready to answer any questions and provide expert assistance. A large range will not leave You without a choice. The company is responsible for the timely delivery. All products are certified. Quality is guaranteed by strict observance of the production technology.